ㅅㅇ
박막형성 공정 실습 (중급) 후기 - 1 본문
SPTA 박막형성 공정 실습 (중급) 2022.03.31-2022.04.01
실습에 앞서 먼저, 1일차 오전 두 시간 정도 이론 수업을 진행하였다.
반도체 기본 지식과 박막 공정에 대해 아주아주 상세히 배웠다. 중급 과정이라 기초부터 심화까지 폭넓고도 깊게 가르쳐 주신 것 같다. 자기소개서 면접과 엮어서 중요한 포인트를 짚어주셔서 더 좋았다.
그만큼 이론 내용 정리하는데 하루 종일 걸렸는데 놓친 부분도 많은 듯 ㅠ 이론 내용도 얼른 문서로 정리해서 업로드 해야쥐
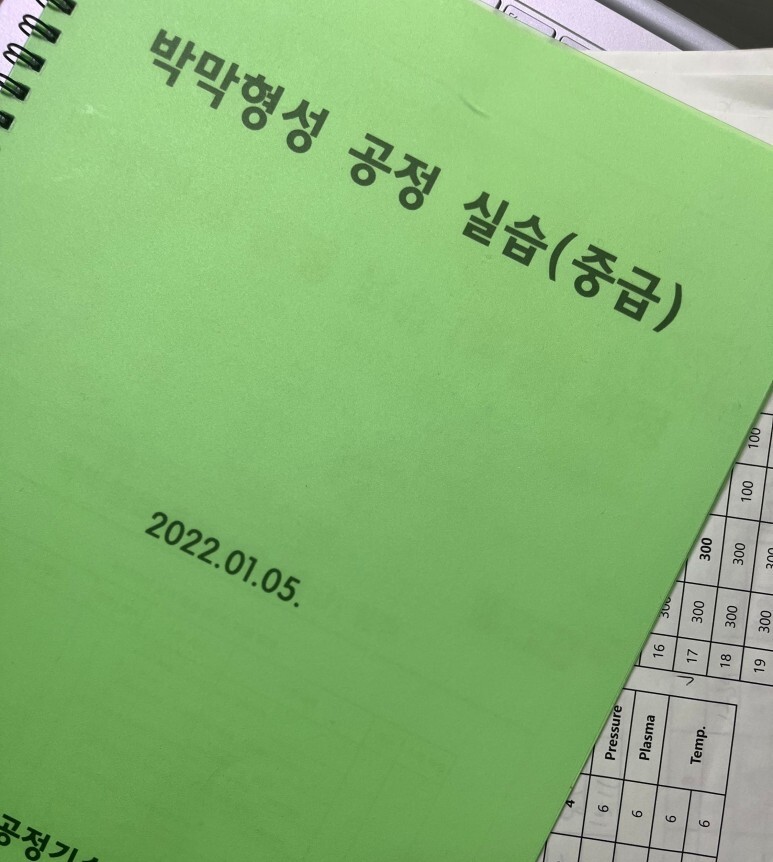

1일차 오후부터 그리고 2일차까지 본격적인 실습을 진행하였다.
<실습 내용>
PECVD SiO2 증착 특성 평가
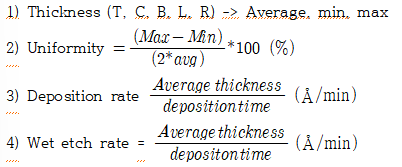
20회 DOE 실험 - Ref 조건을 기준으로 파라미터 별로 양 조절하여 특성 평가
1) Deposition Pressure
2) Plasma Power
3) Gas Flow amount
4) Valance N2
5) Deposition Temperature
6) Annealing 공정 전, 후
- wafer : p type si wafer sub resistivity 10~20
- 반응 gas : SiH4, N2O / Balance gas : N2 0~400sccm
1 SiH4 + 2 N2O -> SiO2 + 2 H2 + 2 N2 -> 조성비 1:2 에 맞춰 2:4 3:6 4:8 spilt
3명씩 다섯 조를 짜서 20회 정도의 공정을 돌아가면서 진행하였다. 다른 실습 교육 경우, 보고 설명듣는 수준이라던데, 여기는 공정을 직접 진행한다는 메리트가 크다.
먼저, 'Clean room'에 들어가기 위해 라텍스 장갑, 방진복, 방진화, 마스크, 머리망을 하고Air Shower를 한 후 입장하였다. Air Shower는 두 개의 문 사이에서 진행되며 한쪽이 닫혀야 다른 한 쪽이 열리도록 되어 있다. 공기의 유입을 최소화하기 위해 room에 들어가기 위해 거쳐야 하는 필수 작업이다. 클린룸은 불순물을 거르고 온도 압력 습도를 잘 유지하여야 하는데 그래서인지 실습실에서 오래 있으니 답답하긴 했다,,
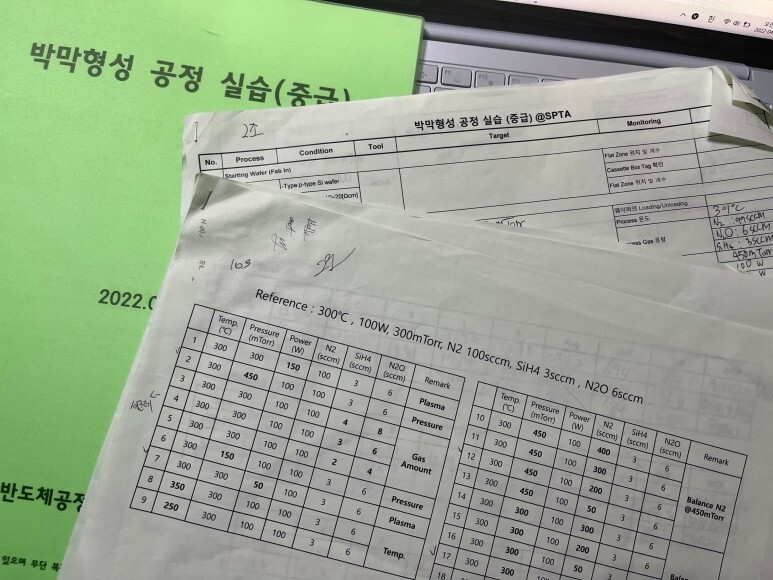
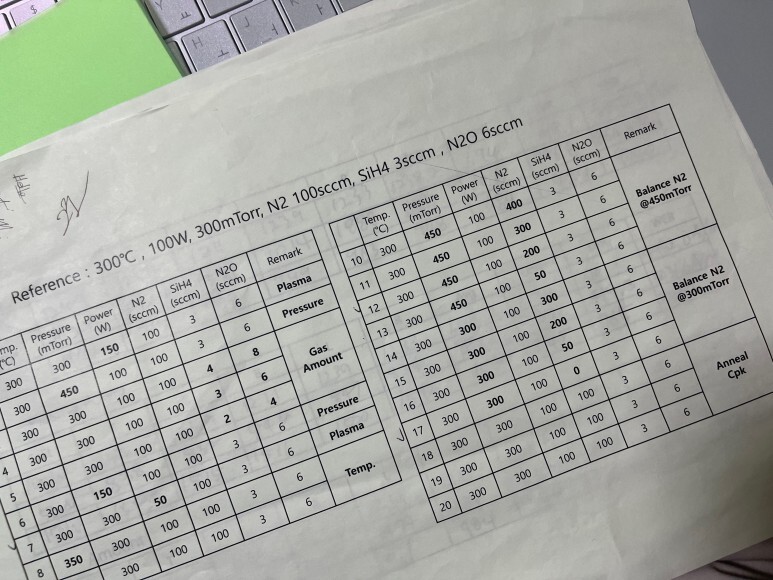
실습 전에 '런시트'를 받았다. 런시트는 일반 종이가 아닌 먼지가 붙지 않는 재질로 되어 있었다. 런시트는 tool, Condition, tool, target, monitoring, remarks 로 이뤄져 있다.공정 순서대로 process이 적혀져 있다. 그리고 condition에는 웨이퍼의 상태, target 공정조건 등을 기입하였다. 본 실습은 SiO Deposition으로 증착 공정 변수 조정에 따라 우리 조가 진행할 조건을 split1, 2, 3, 4 target 공정 조건에 기입하였다. 그리고 tool에는 사용한 장비 PECVD, Wet Bench, Ellipsometer, LPCVD가 적혀져 있다. 그리고 target, monitioring, remarks는 공정을 진행하면서 그리고 진행 후에 계산한 데이터를 적었다.
기나긴 설명 끝에 공정 시작~!
<PECVD SiO2 박막 공정>
장비 제어 순서를 크게 말하면, 진공 -> gas flow -> plasma on 이다.
항상 마지막에 on해줘야 하며, 이 on off가 공정 time을 측정하는 기준이다.이를 먼저 기억하자.
1) wafer loading & 로드락 진공
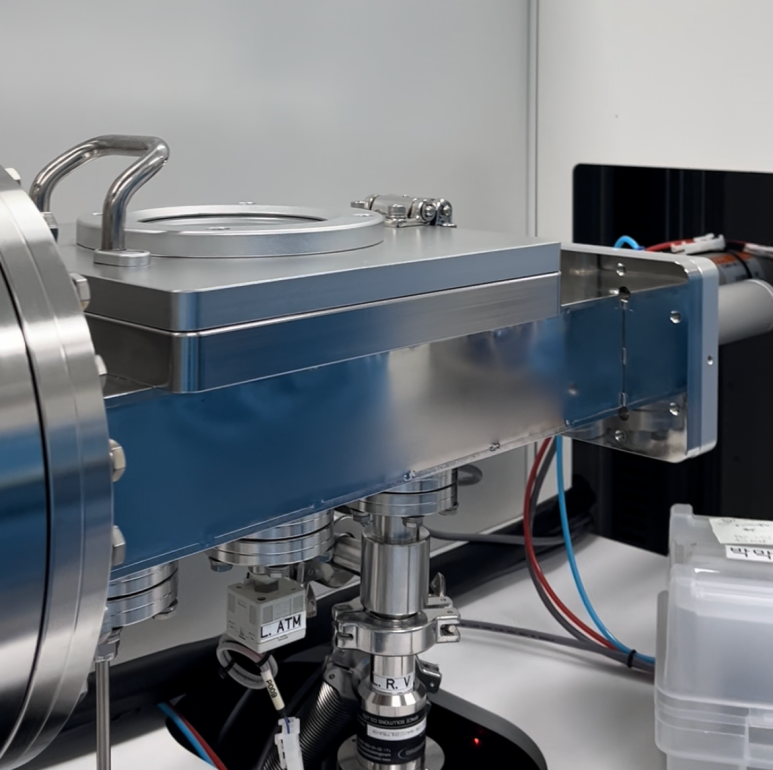
웨이퍼를 load lock에 넣고 loading system을 통해 웨이퍼를 loading 시켜주었다. 원래는 Load port에 있는 웨이퍼 25장을 상압 로버트가 load lock으로 옮겨 준다고 설명을 들었다. 그러나, 우리는 교육용이니 로드 락에 웨이퍼 한 장을 바로 올렸다. 실제 기업 공정에서는 수십장 이상이 한번에 진행된다고 한다.
모든 control은 연동된 pc로 하였다. gui 인터페이스라 사용하기에 편했다.
현재 로드락은 상압이다. 이를 진공으로 만들어줘야 한다. 벨브를 열어, 펌프랑 연결하여 진공을 만들어 준다. 점진적으로 압력이 떨어진다. 로드락 압력이 프로세스 챔버(메인챔버) 압력가 똑같아지는 걸 확인하다. vacuum gauge controller 로드락저진공 화면에서 압력이 떨어지는 것을 볼 수 있다. 압력을 확인하면 벨브를 잠궈준다.
진공 로봇이 로드락의 웨이퍼를 프로세스 챔버로 옮겨야 한다. 그러기 위해 문을 열고 로딩 로버트위에 있는 웨이퍼를 메인 챔버로 로딩해준다. 지금 웨이퍼는 로버트 위에 있다. 들어간 로버트를 다시 꺼내면? 웨이퍼는 그냥 따라 나온다. 당연히 프로세스 챔버에 웨이퍼를 두고 로버트를 꺼내야 한다. 그러기 위해 히터블럭에서 리프트 핀으로 올려준다고 한다. 웨이퍼를 위로 띄어 놓은 후 로버트를 빼고 로버트 들어가려고 열렸던 문을 닫아준 다음 다시 웨이퍼를 내려둔다. 문 닫는 과정이 별 거 아닌거 같지만 만약 안 닫고 벨브를 연다면 최악의 상황이겠지,,
2) 공정 조건 설정 제어
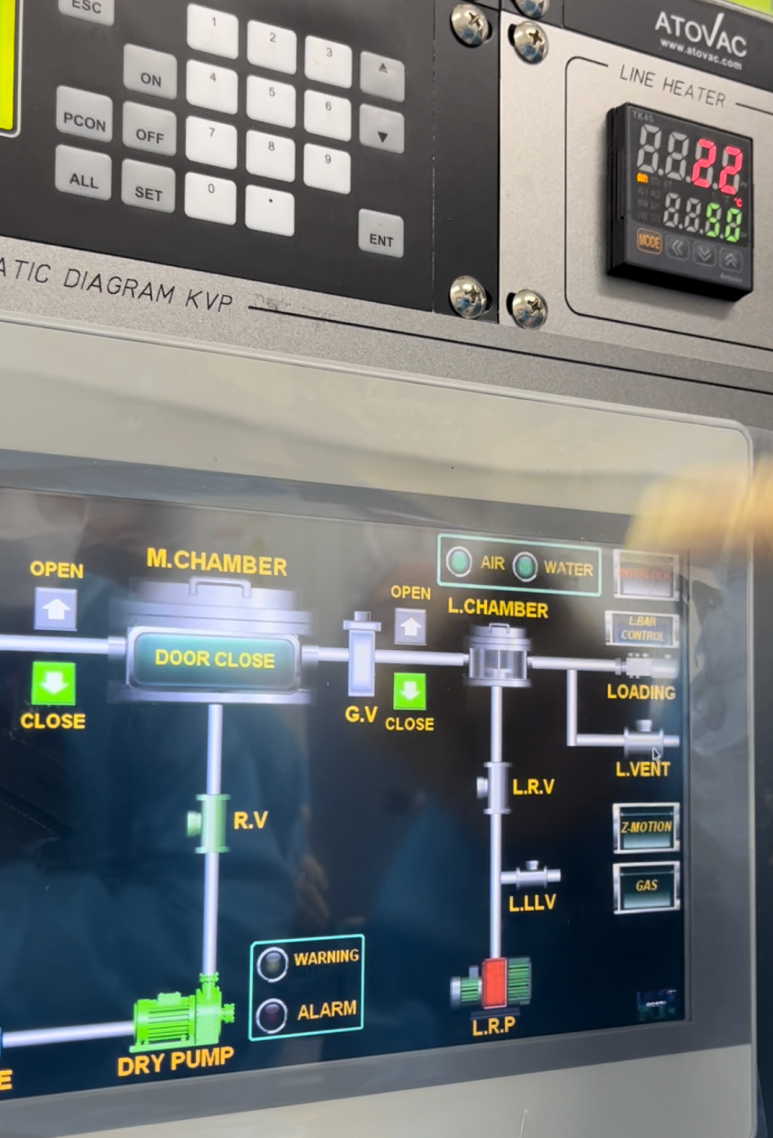
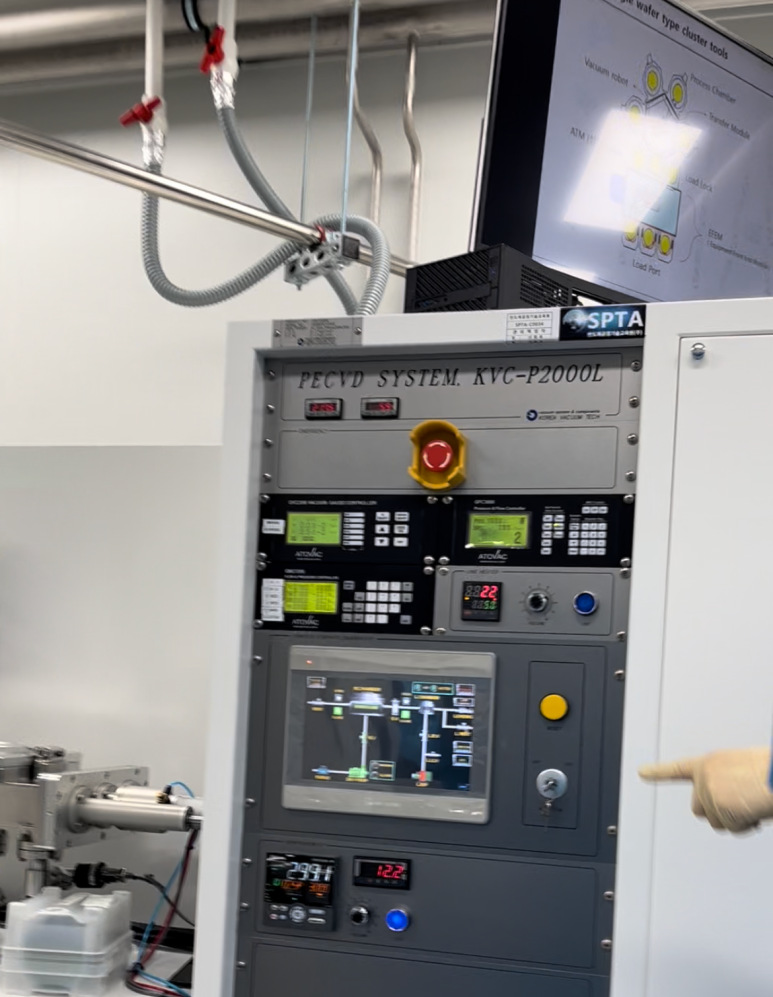
이제 정한 target 공정 조건에 따라 parameter를 조정해준다.
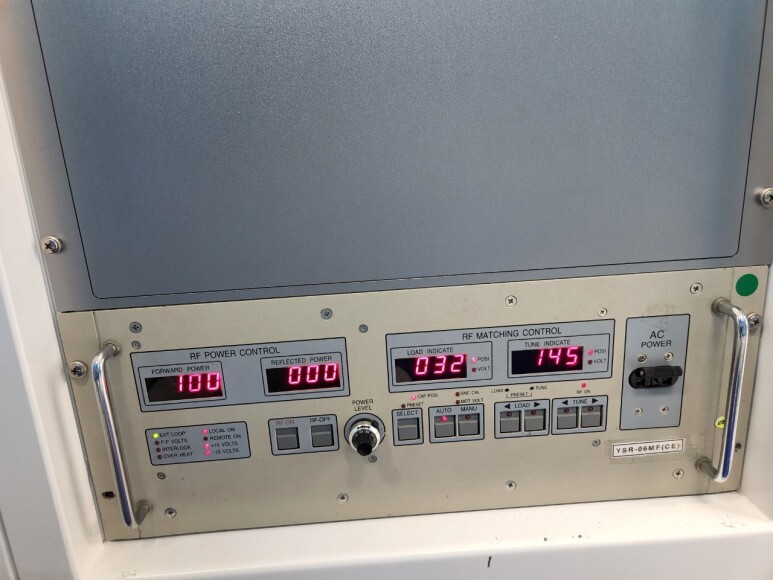
만약 RF power를 바꿔야 한다면 RF on시켜 power를 조정해준다. 이때, 가스는 당연히 흘리지 않은 상태에서 조정만을 위해 잠시 키는 것.!
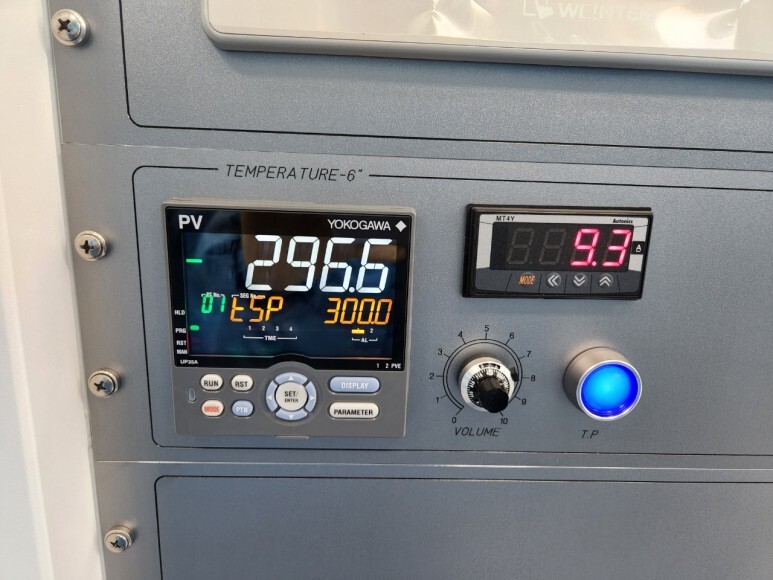
온도도 조정해준다. 우리 조는 온도를 조정하진 않았다.
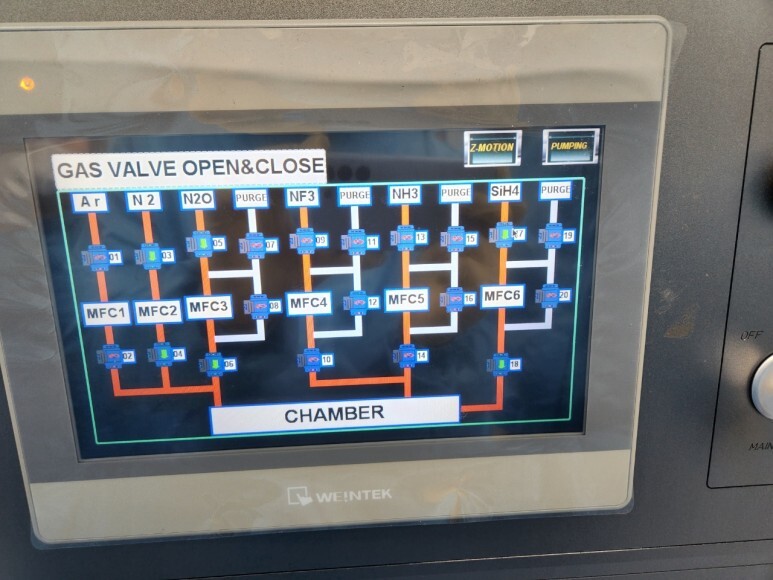
그러고 이제 가스를 흘려줘야 한다. 가스 벨브를 열어주는데 모니터 GUI가 실제 벨브 아이콘으로 이뤄져 있어, 쉽게 열 수 있다.
그리고 유량을 바꿔야 한다면 제어해준다. 이것 또한 몇 번의 클릭으로 가능~.
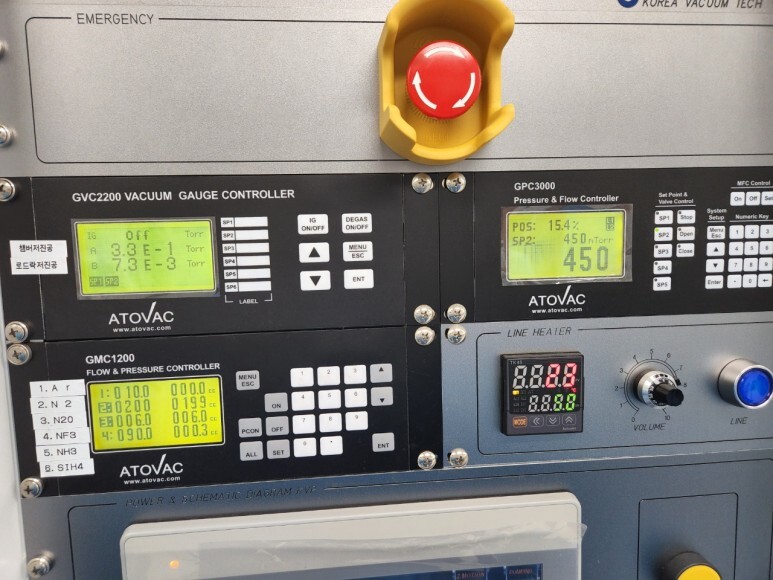
왼쪽이 set point이고 오른쪽이 벨브 열어준 후 실제 흐르는 결과이다. 실제 흐르는 결과 데이터를 나중에 공정 on 후 remarks에 적어줘야 한다. 일단 아직 공정 시작 전으로 Parameter 조정만 해주는 중. 공정 시작의 개념은 plasma on!이다.
모든 가스를 다 흘려 주고 나서, target에 all gas flow 압력을 적어준다. 이는 모든 가스를 흘려줬을 때 압력이며, 최소 압력이다.
이 후 이제 우리가 원하는 공정 압력을 제어해준다.
만약 현재 가스를 흘려준 후 압력이132torr라고 하자. 여기서 우리가 원하는 450torr를 위해서는 버터플라이 벨브를 적절하게 닫게 하여 압력을 맞춰주는 것이다. pos 100% open에서 sp1-sp5를 눌러서 압력을 맞춰준다. 그러고 공정 끝나면 다시 open을 누르는 것.
어쨌든 비교해보자면 300mtorr에서 pos는 14.7% 이고, 450mtorr에서 pos는 10.3% 였다. 14.7%정도가 열려있도록 벨브 pos이 닫히고 그머지 열린 정도로 가스를 내보내 압력을 높인다.
예를 들어, 반응 flow gas가 적다면 all gas flow이여야도 압력이 적을 것이다. 우리 조 실험 중 내가 담당한 실험이 그랬다. N2 gas의 양이 0sccm이였는데 이때 26mtorr였다. 이렇게 저압에서 300torr를 맞춰주기 위해서는 벨브를 활짝 열어야 한다.
이렇게 벨브가 어느정도 열리냐 position이 얼마나 닫히고 있는지 %를 모니터로 확인할 수 있다.
3) 공정 시작 power on

target 공정 조건을 다 설정해주었다면, 공정을 시작한다.
on 누르고 타이머로 진행할 2분을 측정하였다.
on과 동시에 챔버 내 네온 불을 확인할 수 있다. ★exciation & relaxation에 의한 현상인 것을 알아야 한다. 그리고 불의 색깔은 상황에 따라 달라진다는 걸 알아야 한다.
그러고 공정이 진행 중일 때, 재빨리 moritering remarks를 작성한다.
실제 흐르고 있는 가스양(sccm), 온도, 압력, pos, forward power, reflected power, process time을 모니터링으로 확인하고 이를 적어준다.
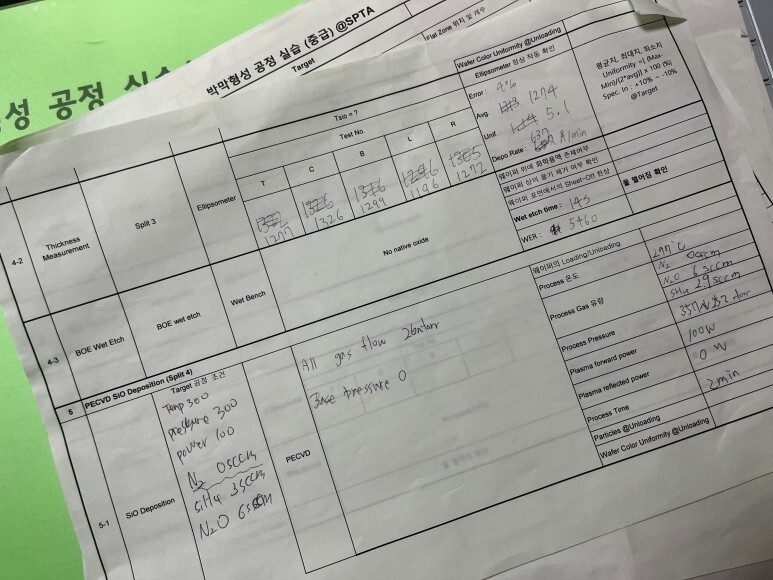
이 과정으로 주요 para를 검증하는 것이다.
이 값과 target 조건을 비교해야, 공정이 정상인지 비정상인지 확인한다. 이렇게 데이터 parameter값을 변화시켜 비교하는 실험에서 공정진행조건는 늘 똑같아야 하므로 target과 동일하게 실제 공정 장비 환경 조건이 되어야 한다.
4) 공정 끝 purge
시간이 지나면 off 누른다. 그러고 위에 압력 open을 눌러 pos 제어해주고 각 가스 벨브를 잠궈준다.
벨브 100% 열고 가스 다 잠구니깐 챔버 안의 압력은 가장 낮은 압력으로 떨어진다. 이때를 base pressure라고 한다.
(만약 base pressure가 12mtorr라면, 공기가 12mtorr를 차지하고 있는 것이다. 장비 내 문제로. 그렇다면 흘려준 반응 가스는 288torr만 차지할 것. 공정, 품질에 영향을 줄 것이다.)
★ all gas flow 시 압력 값과 공정 후 gas 제거 후 압력 base pressure 값은 아주 중요하다고 배웠다.
챔버 안이 300mtorr에서 1mtorr로 됐다는 건 기체몰수가 작아졌다는 것. 그 안에 남아있던 가스가 빠진 것이다.
이를 purge라고 한다. 모든 화학반응 공정은 반드시 purge가 필수이다.
5) 웨이퍼 unloading & 로드락 상압
그러고 이제 웨이퍼를 올리고 문 열어서 로버트 언로딩 in 해준다. 그러고 웨이퍼 내려주고 로버트 꺼낸다. 그러고 문 닫아준다.
그리고 마지막 중요한 것이 로드락의 진공을 풀어줘야 한다. 그렇지 않으면 문 안 열림.
N2 벨브 열어 N2 gas를 흘려줘 상압으로 맞춰 준다.
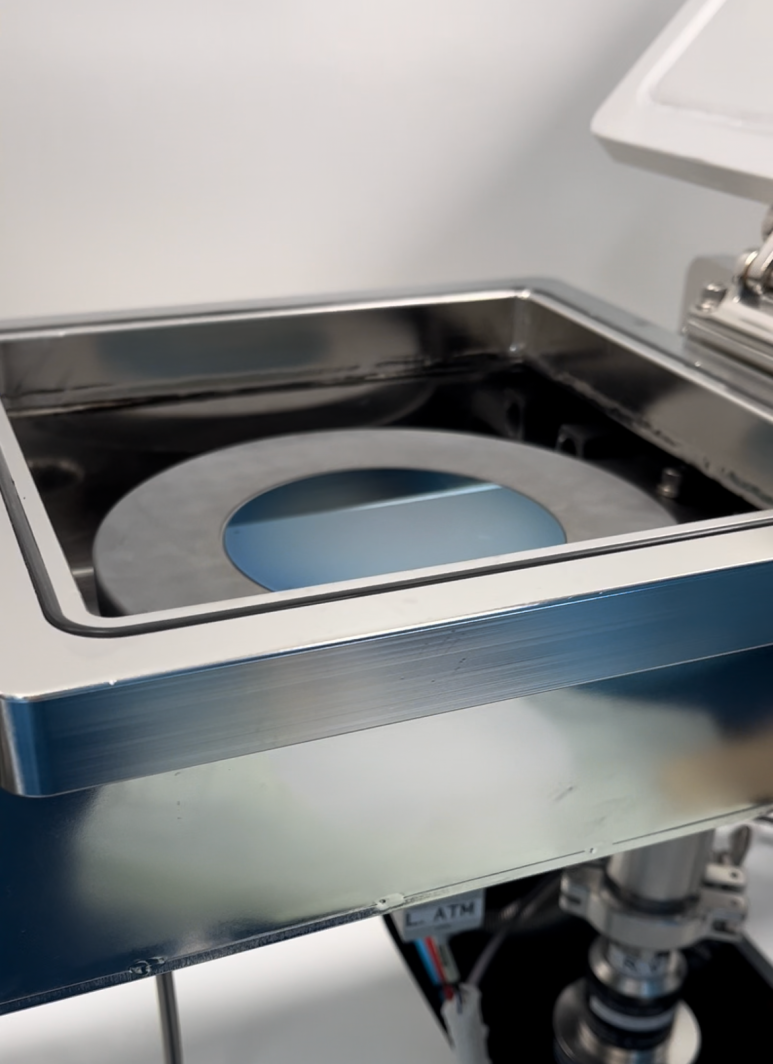
증착 후 웨이퍼 색을 보면 uniformity를 대강 알 수 있다. 색이 가장자리와 중앙이 다르다면 uniformity가 좋지 않다는 것을 육안으로도 알 수 있다. 실제로 우리 조가 진행한 첫번째 실험이 그리하였는데 이를 정확히 두께 측정하니 역시나 균일도가 좋지 않았다.

공정 후 PECVD 챔버 내 쌓여져 있는 oxide를 etch 시켜줬다. 이때 아까 증착 때와 네온 색이 다른 것을 알 수 있다. 광자의 공진주파수 차이에 따라 빛의 색도 다르다는 것을 육안으로 알 수 있다
이제, 박막 공정 후 Ellipsometer를 통해 두께를 측정하였다.
<Ellipsometer 측정>
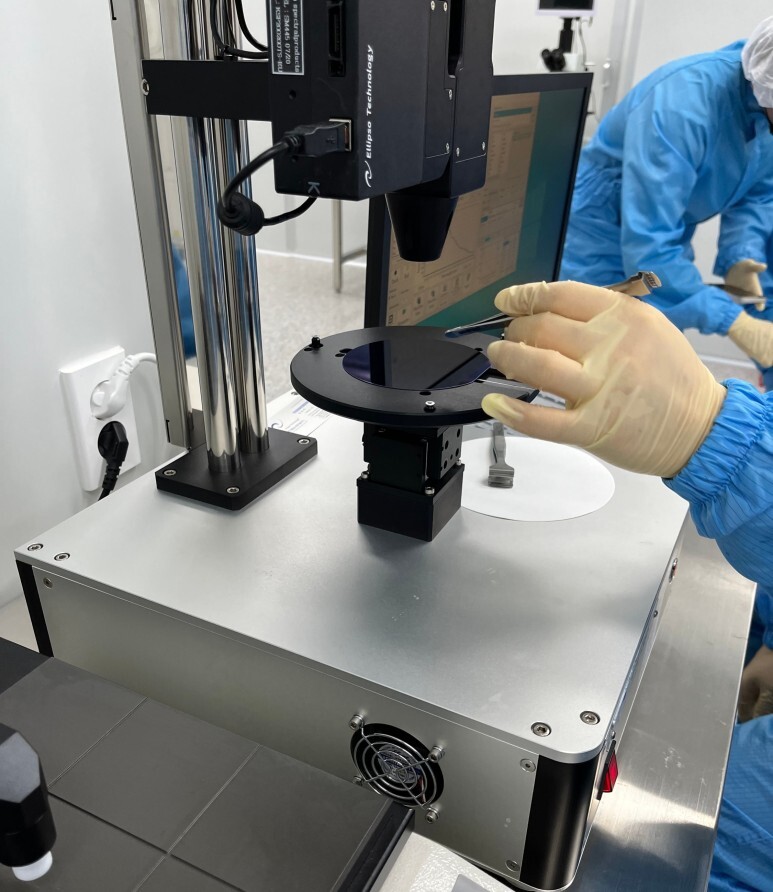
- 편광의 정도를 알고 있는 빛을 측정하고자 하는 물질에 조사시키면 시료 표면에 의해 반사되는 편광상태가 바뀌며, 이 빛의 편광상태를 측정하여 박막의 두께 및 굴절률을 알 수 있다.
- 단파장 보단 주로 편광을 사용.
- 비파괴 분석(시편을 별도로 처리하거나 작은 크기로 자를 필요가 없는 측정)
- 광측정 기술 : 측정 환경에 크게 좌우 되지 않음. 빛이 투과할 수 있는 조건이면 플라즈마, 화학 용액, 극저온에서도 측정할 수 있어 측정 환경에 제약에서 자유로움. 광학장비이지만 암실 필요 x
1) 'Refractive Index 굴절률 확인'
이는 이 장비에서 가장 중요한 point이다.
장비의 굴절률을 꼭꼭 확인해야 한다. 결과로 파장별 RI 값을 모니터링할 수 있다.
즉, 박막 증착 후 두께 측정 시 반드시 계측기 정합성 확인 필요하다는 것이다.
Ri는 어떤 재료가 어떤 조성비로 증착되는지에 따라 달라진다. 그렇기에, 박막의 특성을 알 수 있는 파라미터 중 하나이다.
SiH4는 전압 인가 시 Si≡ 삼중결합으로 존재하기 쉽다. 그래서, SiOx 증착 시 가스 유량비에 따라 넓은 영역의 x값을 갖는 산화막 증착이 가능하다.
stoichiometric SiO RI = 1.46
일반적으로 1.42~1.60 까지의 증착막을 얻을 수 있다.
Silicon Rich SiO RI = 2.14 (Si이 많을 시)
근데 여기서, Si 조성비가 증가하면 RI는 증가한다. Stoichiometric SiO2 막(RI = 1.46) 이상의 Si 조성비를 가질수록 SiOx 막 내에 Si의 dangling bond의 밀도가 증가됨으로 막 내에 H의 농도도 증가하게 된다. 그렇게 미 증착 반응 부산물을 생성시키므로 wafer를 오염시키기 쉽다.
즉, Si content 가 high 일수록 RI 가 크다. 두께 측정값이 틀려지기에 측정 전, RI 값을 확인해야 한다.
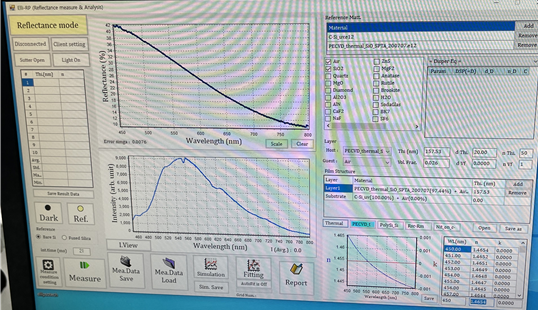
RI 1.4654 -> stoichiometric SiO (SiO2)
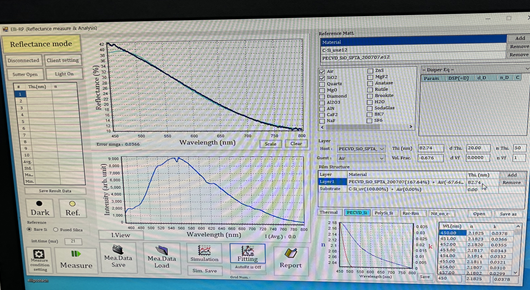
RI 2.1825 -> Si concent 가 많다는 것.
2) 두께 측정
웨이퍼는 항상 'tweezer'를 통해 다뤄야 한다. 이 도구를 통해 장비 위에 웨이퍼를 올리고 T, C, B, R, L 다섯 구역에 대한 두께를 측정하였다. Measure fitting 누르면 위 사진과 같이 굴절률과 두께를 확인할 수 있다. 굴절률1.46 임을 확인하고 두께를 런시트에 기록하였다. error simga값도 기록한다.
그리고 두께 측정 후, 평균치를 구하고 이에 대해 dep.rate와 uniformity를 구한다.
<BOE WET ETCH>
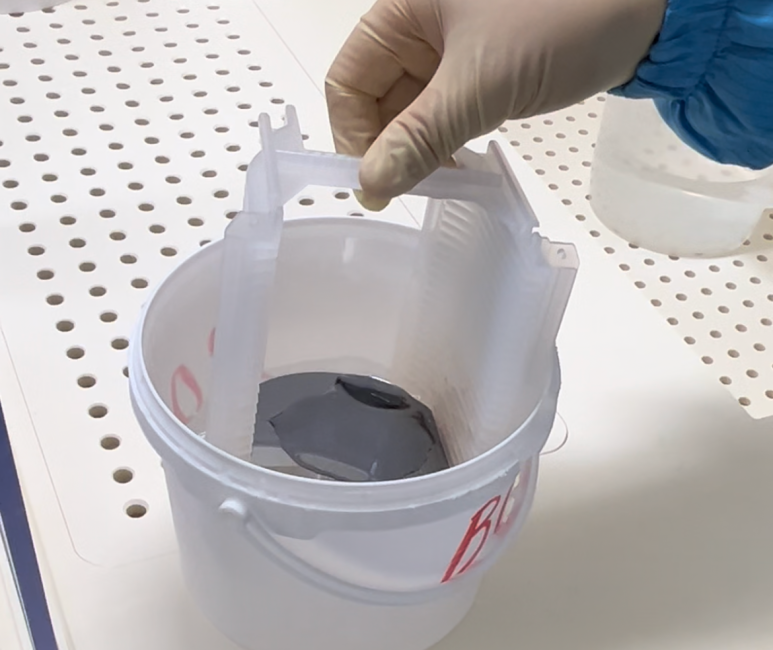
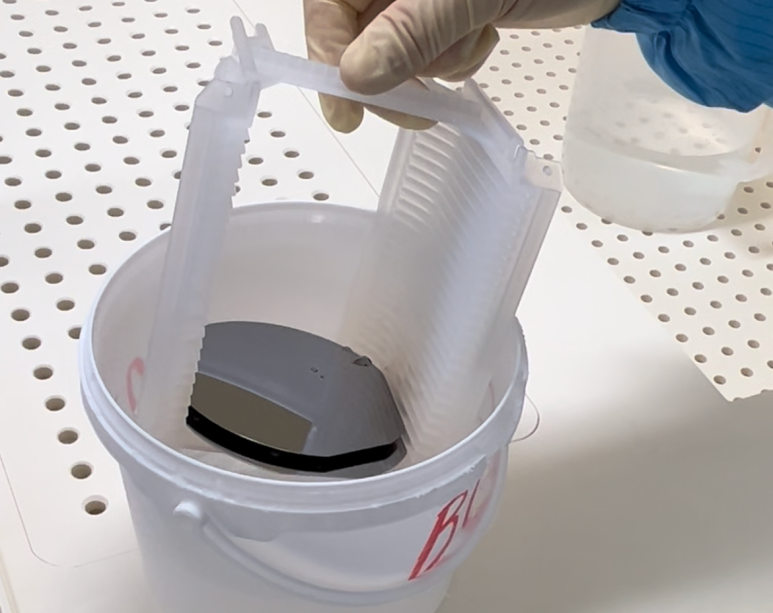
이제, Dep 한 웨이퍼를 BOE를 이용해 wet etch 해보았다.
웨이퍼를 넣었다 뺏다 하면서 ship off 현상을 확인하여야 한다. 처음엔 그냥 젖어있다가 물방울이 굴러떨어진다. 이 현상이 일어났다는 것은 식각 끝이라는 것이다.
이 과정의 시간을 타이머로 측정하여 etch time을 적고 thickness avg.과 함께 계산하여, wet etch rate를 구하였다.
<annealing>
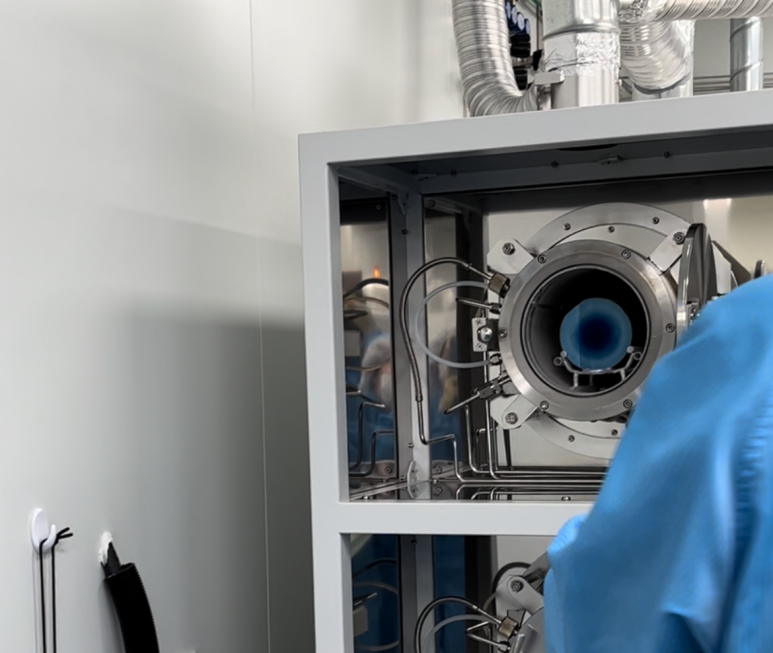
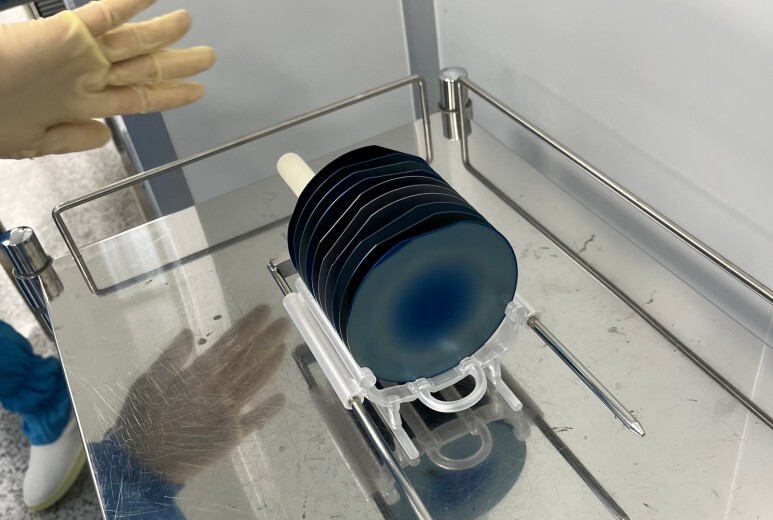
실습 중 하나가 annealing 공정의 유무에 따라 공정 특성을 평가하는 것이였다.
동일한 조건 하에 PECVD를 진행한 웨이퍼 세장에 대해 Anneling 공정을 진행하고 annealing 전과 후에 대해 공정 특성을 비교하였다. annealing은 LPCVD로 650도, 30min로 진행되었다.
(이 공정을 통해서 LPCVD와 PECVD의 공정 차이에 따른 장비 구성 차이까지 알 수 있었다.예를 들자면 LPCVD는 웨이퍼 여러장이라던가)

CVD, ALD 다 고체에서 떨어지지 않는 불순물이 있다. 100% 다 떨어질수가 없다.
Boading length가 title하여 수소가 안 떨어지고 lose하게 결합되어 있다면 O2가 붙지 않기에 SiO2가 만들어지지 않는다. 이를 위해,Annealing이 필수이다.
고체 bibration 되면서 수소가 날아가게 되고 떨어진 Si는 남은 O2와 공유결합하게 된다. 끊어진 구멍난 곳이 채워지는 것.
그러다보니, 친밀해지면서 박막 thinkness가 짧아지고 deposition rate가 낮아게 된다.
그러고, 불순물이 적기 때문에 wet etch rate 또한 낮아진다.
**
LPCVD의 경우, 증착속도가 느리고 온도가 높기에 PECVD에 비해 수소 불순물이 적다. PECVD보다 막질 좋음.
Oxidation의 경우, 온도가 높고 산소를 흘려주는 반응 즉 산화이다. 당연히 이 oxide는 불순물이 제일 적다. 막질이 제일 good.